In the past year, the naira depreciated from N460 to nearly N1500 to the dollar, resulting in a significant increase in the prices of manufacturing inputs. This has worsened the cost of production for local manufacturers, TOBI AWODIPE writes.
In the first quarter of 2023, the Naira exchanged officially for N460 to a dollar and N750 on the parallel market. However, by the time the current administration was sworn in, the Central Bank of Nigeria (CBN) announced the harmonisation of different segments of exchange rates.
The exchange rate has traded between N1,100 and N1,500 to a dollar since March this year.
This situation, industry stakeholders said, has greatly affected the real sector, especially in the areas of raw materials sourcing and imports. The cost of imports has significantly shot up in the last year, with manufacturers saying they cannot continue to produce at the current rates.
According to the Manufacturers Association of Nigeria (MAN) CEOs Confidence Index (MCCI) for Q1 2024 released earlier this month, 100 per cent of manufacturers listed unstable and high FX plus FX scarcity as the greatest challenges hindering production. The report stated that the scarce and high FX is affecting all areas of production, especially in sourcing raw materials and critical inputs needed for production.
About 86 per cent of the MCCI respondents confirmed the increasing cost of production and distribution and 88 per cent decried the increasing cost of shipment as a major factor affecting production. Of the 20 major companies that exited Nigeria in the last 18 months, every single one of them listed FX instability and losses as one of the major reasons for leaving the country.
Data from the National Bureau of Statistics (NBS) said in Q1 2024, raw material imports were valued at ₦1.47 trillion, a significant rise of 164.18 per cent from ₦555.47 billion in Q1 of 2023. While this shows a significant increase in naira terms, the country imported fewer raw materials in Q1 of this year in terms of dollar value. Q1 imports for 2023 stood at $1.21 billion while it was $1.13 billion in Q1 of the year.
Former MAN chairperson, Apapa branch and Chief Executive Officer, Universal Luggage Industries, Frank Ike Onyebu, said this does not come as a surprise as most manufacturers are overburdened by the rising costs of input fuelled by the high cost of FX.
He explained: “This has affected our sourcing of raw materials most of us cannot afford to buy because the rates are very unstable and businesses cannot thrive in an unstable environment. A lot of manufacturers ordered materials when FX was around N1,800 but by the time they arrived, the dollar had fallen a bit. We tried to count our losses and decided to produce at almost cost but by then, the dollar had gone up again. Import duties keep going up, how are we expected to plan or do business in this kind of environment?”
He added that this is the main reason multinationals and major companies are exiting the country, adding: “Those of us that decided to stay are being punished with all kinds of draconian policies that are killing the sector. All these companies shutting down are sacking their workers, leading to further unemployment. Manufacturing is very unattractive currently. Several foreign investors want to come in, but the current business climate is not encouraging. Do you think any right-thinking business would want to struggle with scarce, unstable FX, a depreciating Naira and inability to import or export materials and finished goods?”
He revealed that 70 per cent of materials are sourced locally while just 30 per cent are imported. He said despite ramping up local sourcing of inputs, the local materials have themselves become very expensive and are competing with the imported ones in terms of price.
“One would think that sourcing locally would be cheaper compared to importing but to our dismay, locally sourced materials are almost at par with imported materials. In some cases, they are even more expensive than imported materials. This is another reason businesses are shutting down; when inputs have eaten into all your production costs, what is left?” he asked.
He asked the government to save the real sector from total collapse rather than imposing more taxes and levies on a dying sector.
He added that as part of cost-saving measures, manufacturers have started using recycled materials and have waded into recycling to be independent.
“However, it is not all products we can use recycled materials for, some need virgin materials. Sadly, the petrochemical company that supplies us with materials is more interested in exporting than selling to us locally. They cost the chemicals in dollars to sell to us. A good number of the imported chemicals we import are cheaper than what is sold locally in Nigeria,” he said.
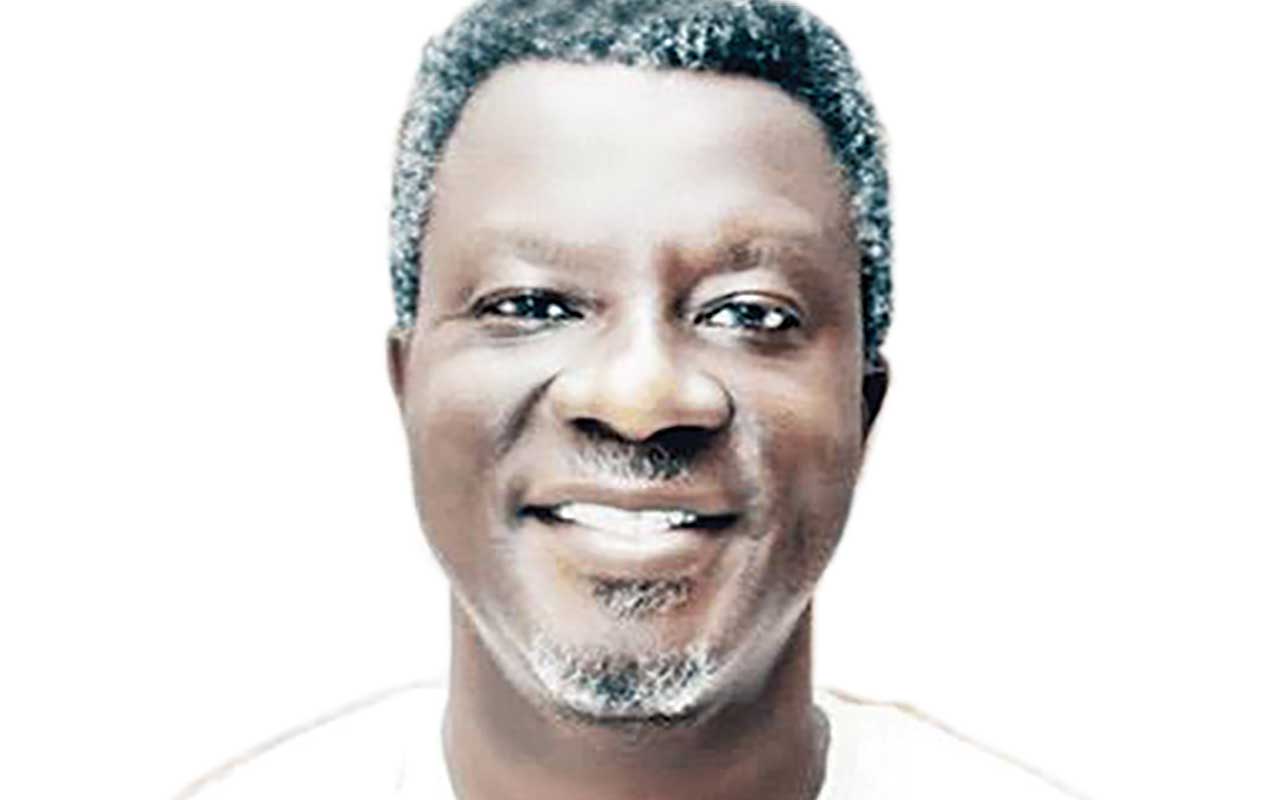
On his part, National Vice President of the Nigeria Association of Small-Scale Industrialists (NASSI) and Chief Executive Officer, Goshen Exquisite Marble, Segun Kuti-George, said despite sourcing just 25 per cent of their raw materials from overseas and the rest locally, the production costs are prohibitive. Lamenting the rising costs of raw materials across industries, he said the raw materials in his industry went up by 50 per cent in the space of six months.
“I need two, three times the amount I was using in Q1 of 2023 to buy the same number of raw materials I need to produce today. We now buy in retail form we can no longer stock anything. If it finishes in the market, we have to wait for the seller to restock and that means no production throughout that period,” he asked.
He added that the locally sourced materials are easily gotten but the price of the imported ones keeps changing daily.
“For my industry, resin is the major ingredient and it is a by-product of petroleum which Nigeria has naturally. Sadly, the resin cannot be sourced locally since Nigeria does not even refine the fuel she uses locally and we are forced to import it. Raw material prices are high because we produce very little. Some people have started trying to look for local alternatives but this will take time and can only be done by big manufacturers, not nano, micro, small or medium industries,” he said.
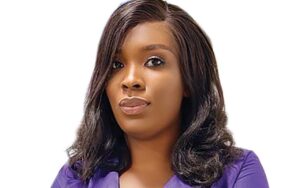
Co-founder, Kazih Kits Limited, Dr Chinedu Azih, lamented that the textile industry has seen an over 500 per cent increase in the cost of raw materials from Q1 of last year till date.
“Every single item we use has shot up and we are only still in business by God’s grace. Makosa material that used to be less than N30,000 for a bundle (30 yards) is almost N50,000 now while a bundle of chinos material that used to be N25,000 is almost N60,000. I don’t even ask or argue about the price again, I just buy what we can quietly.”
Azih said despite sourcing 95 per cent of raw materials locally, the cost keeps going up daily. “The only thing that I can say that we use that is imported is buttons and accessories. We source every other thing locally and yet; the prices are just as if we imported them. The imported materials are very expensive but so also are the locally sourced ones. Many companies have stopped buying boots, they ask their security guards to wear their black shoes. Sales compared from this period last year and now is abysmal, but costs keep going up.”
Azih said the factory where they buy the fabrics complained that they had to import dye, chemicals and other materials used to make fabrics and the unstable FX is affecting the cost of those items.
She stated that as a way to reduce costs, textile manufacturers have embraced textile waste conversion.
She expressed hope that the situation will improve before the end of this year to save the few remaining players still in the textile space.